Establecida en 1992 con un capital social de $ 5,2 millones de dólares de empresas australianas de propiedad exclusiva, y cuenta con una zona de fábrica de 72.000 metros cuadrados.
Molde de tapa
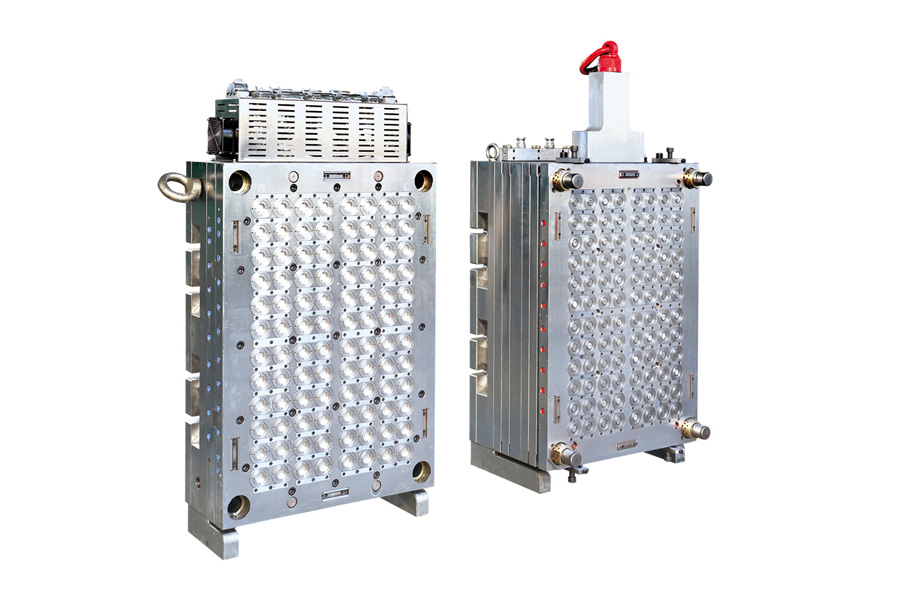
El compuesto del molde 210 se une a la matriz 206 y al marco principal 205. La tapa 220 se une a la matriz 206 mediante un adhesivo 217, y la tapa se une a la matriz con un segundo adhesivo 216. El molde 300 es un dispositivo utilizado en el proceso de moldeo. Funciona junto con el sustrato 200 para producir una serie de paquetes. Tiene dos secciones: una sección de molde superior 302 y una sección de molde inferior 304. La primera está diseñada como una barra de cavidad extraíble, mientras que la última sirve como un molde rígido. La sección de molde superior 302 incluye una pluralidad de extensiones 230 que se extienden desde las esquinas del cuerpo del molde. Las extensiones preferiblemente no se extienden más allá de los bordes del sustrato. Al crear un molde de tapa personalizado, hay varias opciones para crear el aspecto correcto. Una opción es utilizar una serie de moldes rápidos. Estos moldes están hechos para adaptarse a la cabeza individual de un cliente sin problemas ni conjeturas.
Los moldes rápidos han sido probados y han demostrado que funcionan durante años. Otra opción es utilizar gorros de Superhairpieces. Estos moldes están disponibles en 18 tamaños y conjuntos de contornos diferentes, por lo que puede elegir el adecuado para cada cliente individual. Las tapas están etiquetadas con las medidas correctas, lo que facilita colocarlas en la cabeza de un cliente. La máscara de soldadura 116 protege las huellas conductoras de los troqueles semiconductores. Esta cubierta protectora está formada por los procesos de moldeo por transferencia o moldeo por inyección. Además, tienen esquinas achaflanadas que exponen las esquinas del sustrato. Cuando se manipula el sustrato, la máscara de soldadura en estas esquinas es susceptible de agrietarse, especialmente para paquetes de mayor tamaño. La máscara de soldadura es una capa delgada de polímero que generalmente es de color verde. Protege el cobre debajo de la exposición al medio ambiente y evita la oxidación. También evita que crezcan filamentos de metal en la placa de circuito impreso, lo que puede provocar cortocircuitos.
Cuando se diseña correctamente, una máscara de soldadura puede evitar la oxidación del cobre y también extender la vida útil del componente. Uno de los factores clave en la producción de moldeo de tapas es el tiempo de enfriamiento. Puede representar más del 80% del tiempo total del ciclo. La cantidad de tiempo necesario para enfriar una tapa varía según el material, el tipo de ciclo y la forma de la pieza. La Figura 1 presenta una ecuación que se puede usar para estimar el tiempo de enfriamiento. El grosor de la pared y el material seleccionado para el molde juegan un papel importante en la determinación del tiempo de enfriamiento. El ingeniero de diseño de moldes debe asegurarse de que los canales de enfriamiento se coloquen en las mejores posiciones posibles para maximizar la eficiencia de enfriamiento. Además, el ingeniero de procesos debe asegurarse de que las piezas se llenen lo más rápido posible. Si no hay suficiente energía de refrigeración disponible durante las fases de llenado y envasado/retención, las piezas pueden congelarse.